Round screw die is the main component for rolling mill. It suffers from impact during utilization and the surface is rubbed with high speed and high temperature red hard steel. So, the surface should have good abrasive resistance and sufficient tenacity in case of breaking due to impact. For the special purpose of round screw die, the materials should have high speed abrasive resistance, sufficient red hardness, sufficient intensity and toughness. During actual utilization, white cast iron is more appropriate. However, the material is used as cast condition. Casting flaws cannot be avoided and the hardness reaches as high as 50~60HRC. Meanwhile, round crew die has higher requirement for coaxiality which brings huge difficulty for machining.
1. Choosing grade reasonably
Intensity and hardness of materials for round crew die have already reached to common cemented carbide (YT). For this, common materials cannot be machined. Although hardness can be declined properly through thermal refining, convenient for machining, it has higher cost and longer period. Casting cemented carbide is chosen for being machined directly. Through trial cutting and repeated comparison on different hardness, YS8 turning tool is chosen for machining for hardness and abrasive resistance meeting requirements of machining, having lower price. For round crew die requiring repairing, the materials are cold hardened and quenched again and again during utilization. The hardness is quite high. Under the situation that YS8 cannot cut, ceramic turning tool is used for repairing.
2. Choosing mechanical degree and cutting parameters reasonably
Workblank contains Cr, Mo and other elements, having good plasticity, high intensity and hardness, high deformation resistance. Cutting force is higher than common steel by 2~3 times and cutting heat is also growing. The materials have low thermal conductivity, difficulty for heat dissipation, extremely high temperature in cutting area and can be damaged easily. Workblank is casting, having the flaws including scleroderm on surface, pores, sand holes, heterogeneous working allowance and hardness, which resulting in instability increasing, service life declining, cost of production increasing and production efficiency reducing. For these factors, choosing cutting parameters reasonably can improve machining process.
Rough machining
During rough machining, finished surface is uneven and surface of workpiece has scleroderma. Depth of cut should be chosen as large as possible. Depth of cut is deeper, caused cutting heat is higher and cutting force is larger. For sustaining sufficient pressure stress, negative rake and negative side rake (0°~-5°) are chosen to enhance rigidity. Relief angle generally ranges from 6° to 8°. Tool cutting edge angle ranges between 10° and 30°, auxiliary angle 10°~15°. Workpiece has high rigidity and poor heat dispersion. So, low speed (80r/min) is chosen during rough machining. Small feed rate (0.15mm/r) is used to reduce cutting force properly. Depth of cut ranges from 2 to 3mm.
Finish machining
For lower depth of cut, lower cutting force and lower cutting heat, to improve surface quality, larger hook angle are chosen and relief angle uses the maximum value 10°, reducing friction and extrusion with workpiece as much as possible and improving surface processing quality. Tool cutting edge angle ranges from 10° to 30° and auxiliary angle is between 5° and 10°. To prevent processed surface from being scratched by sear metals, positive tool cutting edge inclination (0°~5°), higher speed of mainshaft (120r/min), small depth of cut (0.2~0.3mm) and feed rate (0.1mm/r) are used.
Arc surface processing
When machining excircle, inner bore and overall length, using common lathe is more economical. However, finishing size of arc surface cannot be maintained on common lathe. So, finishing size of arc surface cannot be easily maintained on common lathe. Arc surface of round screw die should be realized by CNC lathe. For uneven margin of workpiece and hard materials, increase times of feed, setting low speed of mainshaft and low feed rate. For the situation that sand holes and pores make cutting head break, set program start pointing before every feed in cases of program starting from beginning after blade breaking, which can reduce time and useless work, highly improving production efficiency.
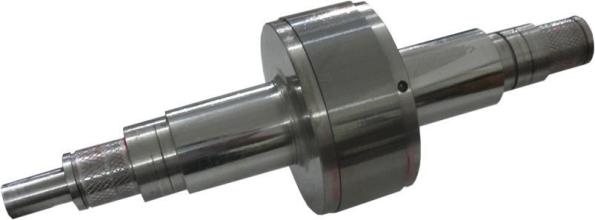