CNC lathe is a kind of automatic lathes having high precision and high efficiency. Equipping with multi-stage knife tower or power knife tower, lathe has wide processing performances, which can process straight cylinder, diagonal cylinder, arc, thread, groove, worm and other complicated parts. It has various offset functions such as line interpolation and circular interpolation, exerting good economic effects in mass production of complicated parts.
During CNC lathe programming, cutting in every process must be confirmed. When choose cutting, all of factors having influences on cutting should be taken into full consideration. Rightly choosing cutting conditions and rationally ensuring cutting can effectively improve quality and quantity of mechanical processing.
In generally, factors affecting cutting conditions include lathe, tool, stiffness of workpiece, cutting speed, cutting depth and cutting feed rate, precision and surface roughness of workpiece, life expectancy and maximum production rate of tool, categories of cutting fluid, cooling methods, hardness and heat treatment of materials, quantity of workpiece and service life of lathe.
Tools made of different materials have different maximum cutting rate. High temperature resistant cutting speed of high speed steel tool is not higher than 50m/min. High temperature resistance cutting speed of carbide toll can exceed than 100m/min while ceramic cutting tool can be as high as 1000m/min. Hardness of materials used for workpiece also has influence on cutting speed of tool. For the same tool, cutting speed should be reduced when cutting hard materials while it can be increased when used to cut soft materials. If tool is required to be used for a long time, lower cutting speed is used. In contrary, higher cutting speed is adopted. The larger depth and feed of cutting are, the larger cutting resistance is and cutting heat is also increased. So, cutting speed should be reduced. Shape, angle and keenness of cutting edge have impact on choosing cutting speed.
For above factors, cutting speed, depth and feed rate are the main factors. Cutting speed has direct influence on cutting efficiency. If cutting speed is too slow, cutting time is extended and tool cannot exert its functions. If cutting speed is too high, tool produces heat easily, affecting service life of tool though cutting time can be declined. Influence of tool materials are the most primary factor having influence on cutting speed. Cutting depth is mainly limited by stiffness of lathe. Permitted by stiffness of lathe, cutting depth should be large as far as possible. If it is not limited by processing precision, cutting depth should be equivalent to working allowance of parts.
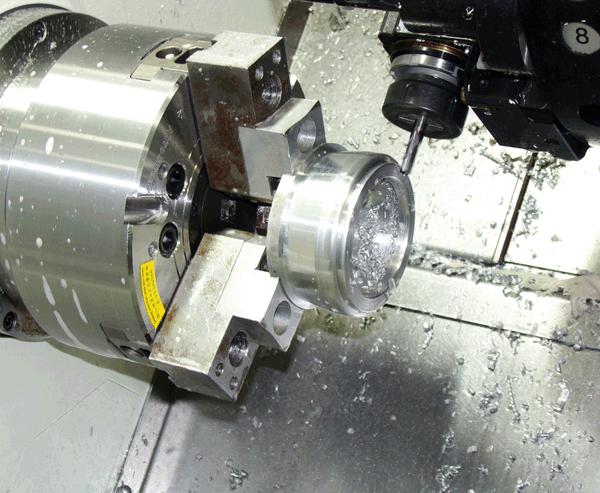