Blowholes on zinc alloy
die casting parts in the electroplate process can be caused by a lot of reasons, such as poor treatment before electroplating, the plating bath containing organic impurities and oil, the bath polluted by the chromium VI and bad matrix metal, etc. The commonly used diagnostic method of blowholes on zinc alloy
die casting parts is listed as follows.
First, scarify the inner cavity which has blowholes of the plating part with a knife. If the combination of coppers is found bad, it is possible that the blowholes are caused by the improper pre-plating process, which made the plating too thin. Then assay the concentration of alkali copper and copper pyrophosphate and find they are in the normal process range. Double the plating time of the alkali copper and copper pyrophosphate and find the blowhole problem still exists after plating.
Put the plating parts in the alkali copper to electroplate for 30 minutes and then directly put them into the acid copper. There are no blowholes formed on the cavity, which indicates that the blowholes may be related to the copper pyrophosphate plating tank. Deal with it with the addition of hydrogen peroxide and yellow-brown foams are found in the process. The operators report that recently, the yellow-brown foams always appear after adding the copper pyrophosphate or potassium pyrophosphate first and then adding hydrogen peroxide, while the foams appeared in milky white in the past. According to the analysis of the phenomenon, it is suspected that copper pyrophosphate or potassium pyrophosphate may be the reason for the blowholes.
After re-preparing copper pyrophosphate and potassium pyrophosphate in the laboratory and having the same test, this phenomenon still occurs while we are adding hydrogen peroxide. Now, we can confirm that there are some problems with the chemical raw materials. Neither dissolving the potassium pyrophosphate and then adding the hydrogen peroxide nor dissolving the original copper pyrophosphate of good quality in a good potassium pyrophosphate will make this phenomenon occur, which proves that copper pyrophosphate is the problem. The solution of this problem is to ask the supplier to replace the copper pyrophosphate with qualified one.
When it comes to electroplating failures, we should not only consider the problems caused by the bath, but also consider the the problems caused by matrix and raw materials. Therefore, this requires us to pay more attention to the detailed problems in the production process, for example, the plating of raw materials should be tested. Add them to the bath if they are tested qualified so as to avoid plating failures and to prevent bringing unnecessary losses for companies.
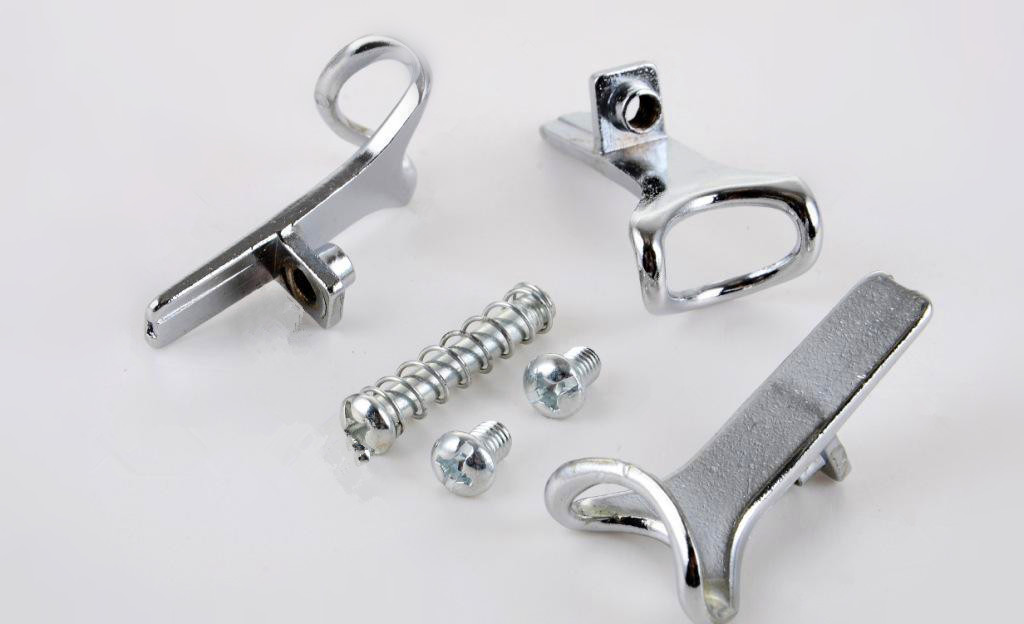